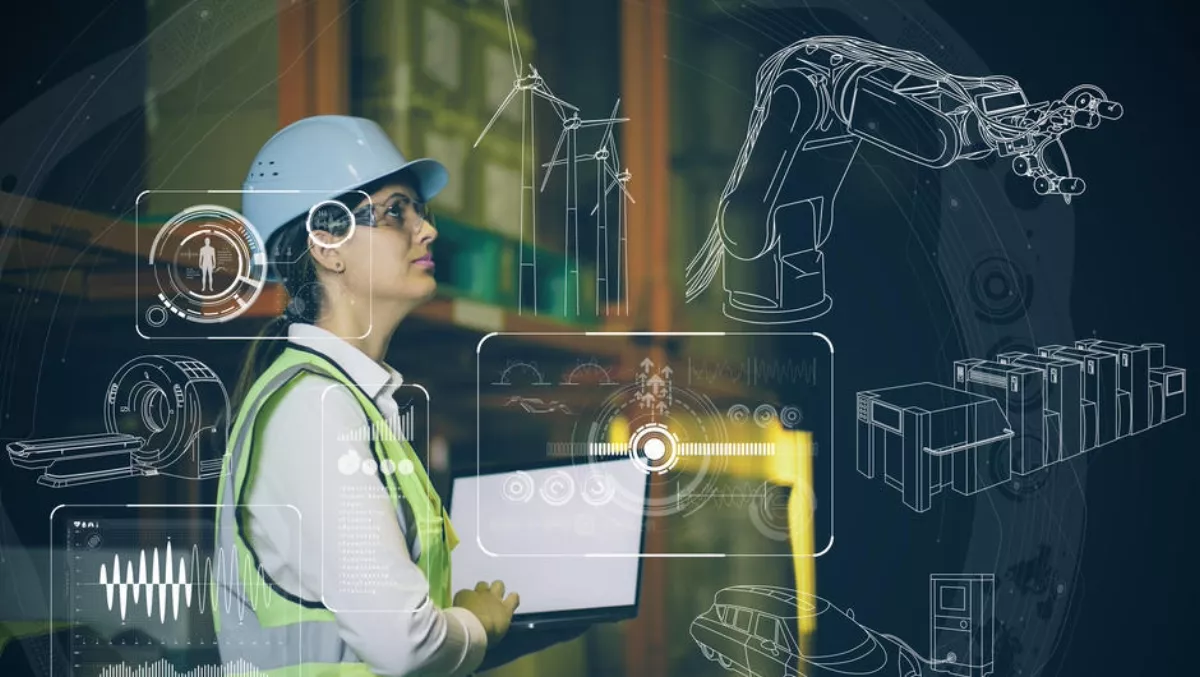
Managing OT cybersecurity vulnerabilities at industrial facilities – PAS Global
The OT vulnerability threat landscape is expanding, rapidly and such vulnerabilities are considerably harder to identify and remediate than IT vulnerabilities.
The sophistication and effectiveness of industrial cyber attacks, such as the Industroyer/CrashOverride malware attack in 2016 and the Triton/Trisis malware attack in 2017 demonstrate that it is more important than ever to identify and remediate OT vulnerabilities.
Even though attacks on OT systems are escalating rapidly, many industrial organisations continue to focus cybersecurity efforts on IT-centric, rather than production-centric endpoints.
They also continue to rely on manual vulnerability management processes, leaving their industrial facilities exposed to unacceptable risks.
IT-centric cybersecurity approaches focus on securing Level 2 endpoints (Perdue model) − operator workstations, servers, routers and switches − as they are much easier to assess than controllers and smart field instruments.
However, focusing on Level 2 endpoints gives only a surface view because they make up only 20 percent of endpoints that exist in process control networks.
Level 1 and 0 systems are often left unassessed.
They comprise 80 percent of the cyber assets in industrial facilities and include distributed control systems (DCS), programmable logic controllers (PLC), safety instrumented systems (SIS), turbine controls, smart field instrumentation, and the sensors that directly connect to process equipment.
Level 1 and 0 endpoints matter the most in industrial facilities because they are responsible for delivering safe and profitable production. However, proprietary architectures and lack of standard protocols in multi-vendor process control environments make asset discovery, vulnerability assessment, and risk mitigation difficult.
This leaves OT systems exposed to vulnerabilities lurking on these underlying systems.
Rising vulnerability counts
The number of vulnerability advisories issued by ICS-CERT has increased by 1,035 percent since 2010.
Many of these vulnerabilities have likely been present for years, only coming to light now due to increased awareness of ICS cybersecurity risk.
OT vulnerability assessment is often a largely manual, point-in-time activity performed by outside contractors once every few years.
Assessments quickly become outdated as systems change, existing vulnerabilities are remediated, and new vulnerabilities emerge.
To maintain currency, OT cybersecurity professionals monitor ICS-CERT and automation vendor websites for new vulnerability advisories or bulletins, and then send emails to asset owners at sites to determine if systems are vulnerable, and if so, what the remediation plans are.
Timely, accurate responses are rare, leaving most organisations in the dark regarding their current risk.
Vendor patches and updates are often not applied for months or years.
What's required is better OT vulnerability visibility and management.
The variety of automation system brands and models running in industrial facilities necessitates a more efficient, standardised approach to OT vulnerability identification and remediation tracking.
Industrial environments need a comprehensive, evergreen inventory of all their Level 2, 1, and 0 systems, including detailed information about current system configurations, firmware versions, operating systems, and applications.
Best practices for OT protection
Manage change effectively: Asset security postures change when process control engineers install new components or perform upgrades and maintenance. Cybersecurity personnel must have an automated way to identify changes and quickly discover any new vulnerabilities.
Look for vulnerabilities all the time: Only automated approaches to OT vulnerability assessment can keep up with the rapidly evolving OT threat landscape so risks to production safety and reliability can be quickly identified. Levels 2, 1, and 0 assessments should occur when new vulnerabilities are published, new systems come onto the PCN, or existing systems are updated.
Prioritise remediation or mitigation: Cybersecurity personnel must prioritise vulnerability remediation or mitigation activities effectively based on potential impacts. Many organisations use the National Vulnerability Database (NVD) Common Vulnerability Score System (CVSS) to gauge the potential impact a vulnerability may have. CVSS scores provide important information about vulnerability exploit ease, potential exploit impact, and if there is known malware that targets the vulnerability. Other factors, such as asset location and criticality to process safety and reliability, should also be taken into account when prioritising remediation actions.
Track vulnerability remediation continuously: Defined vulnerability remediation and mitigation workflows ensure consistent activity tracking and reporting. Viewing the latest data in dashboards and trend views give asset owners, OT and IT cybersecurity personnel the information to make educated vulnerability remediation and cyber risk management decisions.
Stay on top of OT vulnerabilities and risks: Industrial facilities must recognise that vulnerability management is an ongoing, never-ending process focused on risk reduction, not a point-in-time assessment. Continuously reducing cybersecurity risk across the entire environment is what an OT vulnerability management program is all about.
As new vulnerabilities are disclosed and system configurations change, OT systems that were previously secure become insecure.
Organisations that implement continuous OT vulnerability management practices across all their Level 2, 1, and 0 endpoints are best positioned to avoid the danger unseen OT vulnerabilities present to production safety and reliability.